Rolls-Royce develops LiftSystem for the F-35B
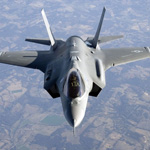
When, in December, Britain’s Harrier jets landed at RAF Cottesmore for the final time, the sombre mood weighed on all those present. In a ritual known as the ’walk of honour’, the pilots disembarked from their aircraft and walked away without taking a single look back.
The walk marked the end of the Harriers’ 41-year career and closed an illustrious chapter in British aviation history. The iconic aircraft has become one of the country’s greatest technical achievements, being the only military jet that could hover above the ground and fly in areas other fighter aircraft were unable to reach.
Despite this capability, the Harrier jets fell victim to the cuts outlined in the government’s strategic defence and security review. The UK has no plans to replace the Harrier and many remain concerned for the loss of military capability. But while the UK may be losing the Harrier, it is not losing the engineering expertise to develop the technology.
At an aero engine test base in Bristol, Rolls-Royce engineers are working on a new power system for the F-35 Lightning II Joint Strike Fighter (JSF), the latest generation of combat aircraft. Dubbed the LiftSystem, the technology will enable short take-off and vertical landing operations for the F-35B variant of the JSF programme, which is planned to enter service with the US Marine Corps in 2012.
The LiftSystem will allow a fighter aircraft to achieve both vertical lift and supersonic capabilities. Like the Harrier, the F-35B will be able to land without a runway and take off like a helicopter, while performing as a fighter aircraft. At the heart of the system is a component known as the Liftfan. This a 50in (127cm), two-stage, counter-rotating fan capable of generating 20,000lb (9,000kg) of thrust. Situated just behind the cockpit, it produces the aircraft’s forward vertical lift. ’The Liftfan is effectively an engine turned on its end,’ said Neil Mehta, programme director. ’This means the air has to turn through 90° before entering into the aircraft, causing huge distortions in airflow.’
A normal aircraft engine is usually cleared to around a 30-knot cross wind. The F-35B, however, has to deal with winds up to 300mph (483km/h). ’To put that into context, Hurricane Katrina measured at about 75mph at its max, so we’re getting an awful lot more distortion,’ he said. To address this, the team has used computational fluid dynamics to model airflow behaviour and aerodynamic performance.
’Our programme for one cycle of the simulation uses as much processing power as a PlayStation running for 14 years,’ said Mehta. ’We’ve done more than 1,000 of those simulations.’
Designed around the airflows are two counter-rotating bladed discs, or ’blisks’, manufactured using individual hollow blades joined to the disc through linear friction welding. The blisks take air from the top of the fuselage and blast it through a vane box at the bottom of the craft. Each vane box can be directed independently, so the air can be generated fore and aft.
At the rear of the aircraft, thrust is produced from a rotating nozzle known as the three-bearing swivel module (3BSM). In normal flight, the nozzle points rearwards, propelling the aircraft forwards at speeds of up to Mach 1.6. When vertical thrust is required, the nozzle swivels downwards in less than two seconds, creating a vertical thrust of up to 20,000lb, equalling the force generated by the Liftfan.
Stabilising this force are two small ’roll posts’ in the wings. These ducts each direct 2,000lb of thrust during short take-off and vertical landing. Compact flap mechanics regulate the amount of thrust produced by each of the roll posts. During short take-off, the roll posts are opened and the clutch is engaged, the 3BSM is swivelled
’One of the big challenges for the LiftSystem is that we only use it for short take-off and landing,’ said Mehta. ’In a normal mission, that is only around five per cent of the total activity. So, at that point, we have to make sure the system is low weight, otherwise it’s not earning its keep in there.’
For the blisks, Rolls-Royce is using hollow titanium blades. The technology, derived from civil turbofans, cuts weight by around 40 per cent. Mehta said the current version of the LiftSystem is about 320kg lighter than the original demonstrator but is also stronger and more reliable.
He added: ’This time last year, we did our first hover and first vertical landing. Those two events were the start of proving that all our work the preceding year was accurate. We did vertical landings and nothing untoward happened. We’ve since done 58 vertical landings, 79 hovers, 90 slow landings and 95 short take-offs, and nothing has gone wrong.’
Orders for the LiftSystem are expected to total more than 600, and the US Marine Corps and the Italian Navy have already acquired the system. There are still several years of flight tests remaining, and shipborne trials are due to take place later this year. Production of the system for use in training aircraft is under way and Rolls-Royce is delivering one LiftSystem per month.
Mehta said the UK is in a strong position to continue developing the technology. ’We developed the Pegasus engine that goes in the Harrier, and we’ve now developed the LiftSystem,’ he said. ’There are no other Western countries with that kind of expertise.’